Creating Efficient Work Orders for Automotive Parts
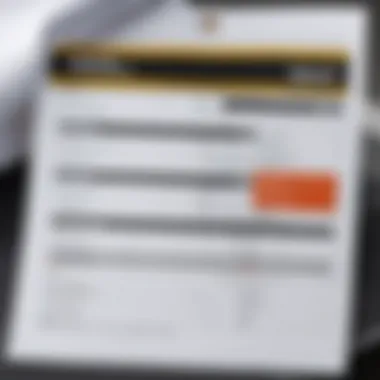
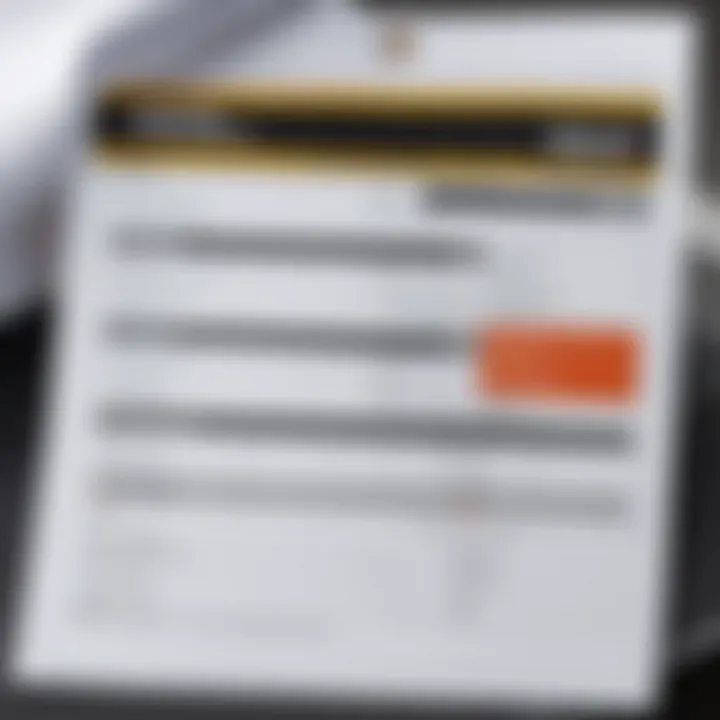
Intro
Creating a work order for part installation is crucial in the automotive industry. This process not only streamlines the maintenance and repair workflow but also ensures that customers receive quality service. In this guide, we will examine the various steps involved in drafting a work order and the essential components that make it effective. Understanding these elements is particularly important for automotive enthusiasts and professionals seeking to enhance their skills.
Обзор автомобиля
In order to create an effective work order, it's essential to have a clear understanding of the vehicle involved. Knowledge about vehicles can impact how orders are formulated and executed.
Основные характеристики
Different vehicles possess distinct characteristics which affect part selection and installation. These traits include the make, model, and year of manufacture. For instance, a 2020 Toyota Camry will have different specifications and parts than a 2015 Ford Mustang. These variations influence the type of work order generated.
Описание двигателей и трансмиссий
Understanding the engine types and transmissions is also vital. Vehicles with gasoline engines may require different parts compared to those with diesel options. Moreover, the type of transmission, be it automatic or manual, will further dictate the necessary installation procedures. Accurate knowledge in this area ensures that the correct work orders are created, minimizing potential errors during part installation.
Выбор автозапчастей
Once the vehicle specifics are determined, the next step involves selecting suitable auto parts. This selection is paramount for a successful repair or maintenance process.
Разновидности запчастей
Automotive parts can be categorized into various types. Original Equipment Manufacturer (OEM) parts are those that match the specifications of the vehicle as provided by the manufacturer. Aftermarket parts, however, are produced by third parties and can vary in quality. Understanding these differences helps in making informed decisions when drafting work orders.
Как выбрать качественные запчасти
When choosing parts, consider factors such as reliability, warranty, and cost. Researching product reviews or manufacturer reputation can provide insight into the quality of parts. It's essential to select parts that will not only fit the vehicle but also provide the desired performance. Creating a work order becomes much more manageable when these components are considered carefully.
Understanding the vehicle and selecting the right parts are key steps in creating an effective work order for part installation.
Prelims to Work Orders in Automotive Services
In the context of automotive services, work orders serve as a crucial framework for managing repairs and installations. They encapsulate the necessary information required for technicians to execute their tasks efficiently. The significance of developing a precise work order cannot be overstated. It acts as a contract between service providers and customers, detailing what services will be performed, along with the associated costs.
The creation of a work order promotes clarity within the workflow. When technicians understand their responsibilities and the specifications of the task at hand, it reduces the potential for errors. An accurately created work order ensures that each aspect of the service, from part identification to installation details, is meticulously documented. This encourages accountability among service personnel and helps safeguard against misunderstandings that can arise from vague instructions.
Moreover, work orders facilitate better communication between different departments within an automotive service facility. A clear outline of the tasks allows parts departments to prepare the necessary components beforehand. Technicians can work in an organized manner, reducing downtime and increasing overall productivity. Overall, work orders are an essential component in streamlining automotive operations, aligning the efforts of technicians, parts suppliers, and management toward common objectives.
Definition of a Work Order
A work order can be defined as a formal document that requests a specific service or task to be completed. In automotive services, this means detailing what needs to be done on a vehicle, specifying the parts required, and often includes the customer’s information and a brief description of the vehicle's issues. A well-structured work order helps to ensure that no important detail is overlooked during the repair or installation process.
Importance in the Automotive Industry
The automotive industry places a high premium on efficiency and reliability, both of which are significantly enhanced through the use of work orders. First, work orders allow for informed decision-making. When technicians have access to the necessary information in one document, they can prioritize tasks better and optimize their time on the job. This leads to faster turnaround times, which is critical in a competitive environment.
Second, with a clear work order, there is a documented history of repairs and parts usage that can be invaluable for future reference. This historical data helps mechanics identify recurring problems, guiding them in preventive measures. Furthermore, having a structured work order system can significantly improve customer satisfaction by ensuring transparency in service processes. Clients can see exactly what work is being done on their vehicles, which fosters trust in the service provider.
"A well-written work order is not just a set of instructions; it's a roadmap to successful automotive service."
The combination of these aspects makes work orders indispensable not only for efficiency but also for maintaining standards of quality in automotive repairs.
The Structure of a Work Order
Understanding the structure of a work order is essential for ensuring that automotive services run smoothly. A well-organized work order serves as a communication tool between various departments, enabling precise tracking of repairs and maintenance tasks. This clarity not only streamlines operations but also enhances accountability and efficiency within the automotive service workflow. Moreover, a structured work order enhances the overall customer experience by providing accurate estimates regarding timeframes and costs associated with the service.
Essential Components of a Work Order
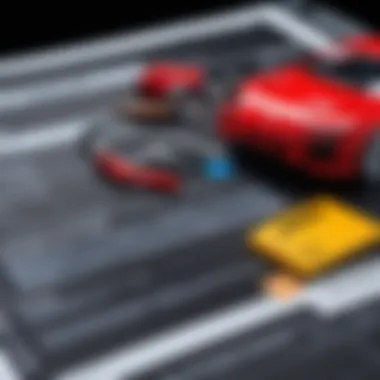
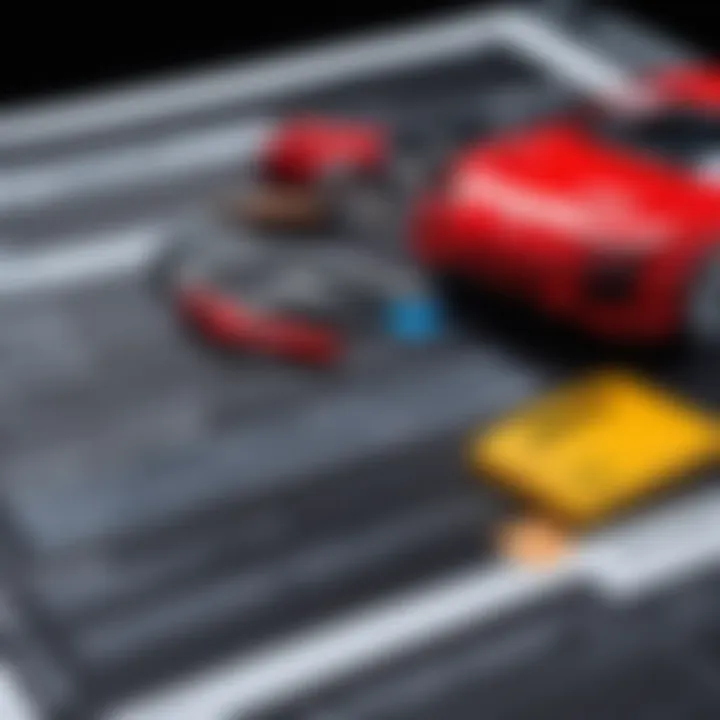
A complete work order consists of multiple components that collectively outline the tasks to be undertaken. Here are the essential elements that should be included in every work order:
- Work Order Number: Each work order should have a unique identifier. This simplifies tracking and reference.
- Customer Details: This includes the customer’s name, contact information, and vehicle details like make, model, and VIN. Having this information helps tailor the service specifics to the client's needs.
- Service Description: A clear description of the work to be done is vital. This section should detail the specific parts being installed and any necessary repairs to avoid ambiguity.
- Parts Required: It is crucial to specify the parts needed for the service. This ensures that technicians have all necessary components at hand prior to starting the job.
- Technician Assigned: Including the name of the technician responsible for the installation promotes accountability and direct communication.
- Estimated Time of Completion: Providing a timeline for how long the work will take can help manage customer expectations and improve scheduling efficiency.
- Status Updates: Regular updates on the work process should also be documented. This helps keep all stakeholders informed.
Each of these elements contributes to the clarity and functionality of the work order, enabling smoother operations in the automotive service sector.
Common Terminology Used
In the creation of work orders, specific terminology is frequently used to ensure everyone involved understands the processes and requirements clearly. Here are some common terms:
- Work Order (WO): The formal document requesting specific services to be performed on a vehicle.
- Service Request (SR): A preliminary document that outlines what a customer is requesting before a work order is generated.
- Parts List: Overview of all components that need to be replaced or installed.
- Job Code: A code that aids in categorizing the type of service requested, often for tracking and reporting purposes.
By providing clarity through well-defined components and terminology, a solid structure enhances the efficiency of automotive services. Understanding this structure allows automotive professionals to execute repairs and installations with significantly less room for error.
Steps to Create a Work Order for Part Installation
Creating a work order for part installation is a critical aspect in the automotive industry. This process not only ensures that services are rendered efficiently but also helps prevent common errors that could lead to costly delays or repetition of tasks. In this section, we focus on the main steps that lead to a well-structured work order. Each step plays a specific role in ensuring clarity and efficiency in the installation process, which benefits both the automotive service provider and the customers.
Identifying the Required Parts
The first step in creating a work order is identifying the required parts for the installation. This act requires careful consideration of the vehicle's specifications and the nature of the repair or maintenance work being performed. Proper identification minimizes the chances of delays caused by incorrect or missing parts.
To start, technicians need to conduct a thorough assessment of the vehicle. This can include:
- Performing a diagnostic check to determine malfunctioning components.
- Consulting service manuals that detail part specifications.
- Collaborating with other team members to gather insights about previously used parts.
An efficient inventory system can aid in this process by indicating stock levels and compatibility of parts. By compiling a precise list of required parts right at the onset, effective communication with suppliers for timely procurement can occur.
Documenting the Installation Details
After parts have been identified, the next step is documenting the installation details. This documentation should be thorough yet concise, as it defines the scope of the installation work. Key elements to include are:
- Specific installation instructions: Clear directives regarding how the parts should be installed.
- Tools and equipment required: Listing of necessary tools can prevent last-minute scrambling.
- Safety protocols: Ensuring that all safety regulations are included safeguards team members while they work.
This documentation serves as a reliable reference for technicians during the installation process. It also functions as a record that can be referred back to in future maintenance or inspections, ensuring a smooth workflow.
Assigning a Technician
Assigning a technician to the work order is the next crucial step. This decision can impact overall efficiency, so careful consideration is necessary. Factors to consider include:
- Skill level: The technician’s experience and familiarity with the specific type of installation.
- Current workload: It is essential to assess the technician's availability to meet the deadlines without compromising quality.
- Specialization: Some parts may require specialized skills, so targeting the right expert can lead to more effective and efficient installations.
Having a clear assignment fosters accountability, as it is evident who is responsible for which tasks. This not only promotes a smoother workflow but also enhances the quality of the work performed.
Setting a Timeline for Completion
The final step focuses on setting a timeline for completion. Establishing a realistic timeframe is vital, as it impacts service responsiveness and customer satisfaction. When determining the timeline, several considerations must be taken into account:
- Complexity of the installation: The more complicated the installation, the longer it may take. Detailed evaluations should guide this.
- Availability of parts: Ensure parts are on hand as scheduled deliveries can affect completion.
- Technician's schedule: Ensuring the technician has enough time allocated in their schedule is critical for adherence to the timeline.
It can be useful to incorporate buffer times to accommodate unforeseen delays while still maintaining a realistic target. Clearly listing the expected timeframe in the work order enhances overall transparency and keeps both technicians and clients informed.
To sum it up, clearly defined steps lead to effective work order creation, enhancing efficiency in the part installation process and ensuring that automotive services are delivered competently.
Software and Tools for Work Order Management
In today's fast-paced automotive industry, effective work order management is crucial for maintaining operational efficiency. Software and tools designed for work order creation and tracking streamline this process. These solutions help in organizing tasks, tracking parts, and ensuring that all details are accounted for. The significance of these tools cannot be overstated, as they reduce human error and enhance the ability to meet deadlines.
Popular Work Order Management Systems
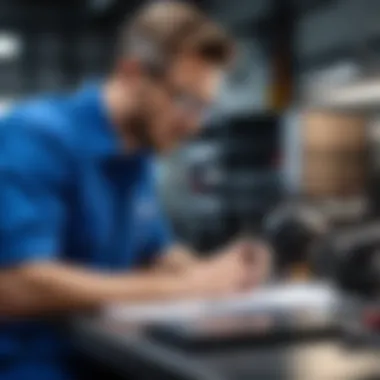
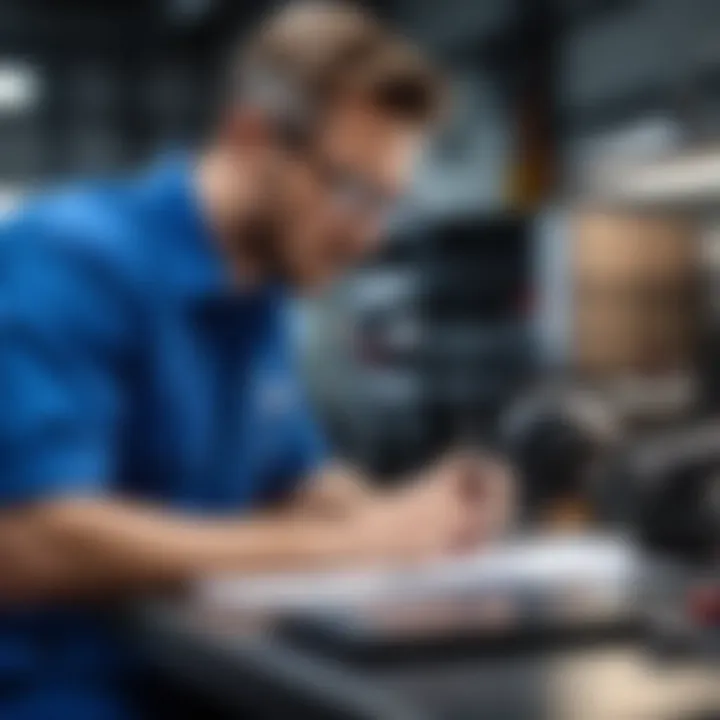
Several work order management systems are available that cater to the diverse needs of automotive professionals. Two notable examples are Shop-Ware and Mitchell 1. These systems offer various features that simplify the management of work orders.
- Shop-Ware: This system provides an integrated approach with customer management and inventory tracking. It helps in creating detailed work orders and allows team members to view ongoing tasks in real-time.
- Mitchell 1: Known for its extensive database, Mitchell 1 offers a variety of services, including the creation of work order templates. It enhances communication among team members by providing insights into parts availability and labor times.
These systems not only ease the documentation process but also improve collaboration among departments, leading to a more efficient workflow.
Integrating Software with Inventory Systems
Integrating work order management software with inventory systems is essential. This integration ensures that information flows smoothly between different parts of the operation, allowing for better tracking and management of resources. When these systems are connected, it enhances the visibility of stock levels, making it easier to manage supply and demand effectively.
For example, using software like AutoFluent can help link work orders with inventory control. This ensures that when a work order is created, the system can access real-time inventory data. This avoids any delays caused by stock shortages and keeps operations running smoothly.
In summary, the integration of work order management tools with inventory systems not only streamlines processes but also allows automotive businesses to respond to customer needs promptly.
Effective coordination between work orders and inventory management significantly impacts the efficiency of automotive operations.
Best Practices for Creating Effective Work Orders
Creating effective work orders is critical for the smooth operation of automotive services. An effective work order contributes not only to thorough documentation but also enhances communication among team members. The following best practices aim to ensure clarity, efficiency, and overall success in managing work orders for part installation.
Clarity in Communication
Clear communication is a cornerstone of effective work order management. It minimizes misunderstandings and provides all parties involved with a precise understanding of tasks and expectations. Each work order should contain detailed descriptions of the work to be performed, including:
- Specific Part Information: Include make, model, and any part numbers associated with the installation tasks.
- Step-by-Step Instructions: Lay out the exact steps required for installation, preventing misinterpretation by technicians.
- Expected Outcomes: Define what a completed installation looks like. This helps set expectations.
Using straightforward language avoids confusion. Technical jargon should be explained or minimized whenever possible to ensure everyone on the team comprehends the work order fully.
"Clear and concise work orders are not just helpful; they are essential in preventing costly errors and enhancing productivity."
Regular Updates and Follow-Ups
Regular updates and follow-ups play a vital role in keeping the work order process on track. Establishing routine communication regarding the status of ongoing installations can prevent delays and improve workflow. Consider these points:
- Scheduled Check-Ins: Designate times to review the progress of installations, allowing for adjustments as necessary. This could be daily or weekly, depending on the volume of work.
- Document Changes Promptly: If any changes are made to the work order, they should be recorded immediately. This prevents confusion and ensures everyone involved is aware of the latest instructions.
- Feedback Loop: Encourage technicians to provide feedback on the work order process. Their insights can identify potential issues and enhance future orders.
Implementing these communication strategies fosters a collaborative environment that can significantly improve the efficiency and effectiveness of work orders in the automotive industry.
Common Challenges in Managing Work Orders
Managing work orders for part installations in the automotive industry is essential for successful operations. However, numerous challenges arise during this process. Understanding these challenges is critical to improving efficiency and ensuring seamless collaboration among teams. Tackling these issues enables businesses to streamline workflows, minimize errors, and enhance customer satisfaction.
Miscommunication Between Departments
Miscommunication between departments is one of the primary challenges faced in managing work orders. When various teams, such as service, repair, and parts, fail to communicate effectively, it can lead to significant misunderstandings. This scenario often results in the wrong parts being ordered, delays in service, and ultimately, customer dissatisfaction.
To mitigate these risks, it is vital to establish clear lines of communication among departments. Utilizing advanced work order management systems can facilitate this communication. Tools like Shop-Ware or Mitchell 1 allow different departments to access relevant information in real-time. Moreover, regular meetings can assist in discussing ongoing projects and identify potential issues before they escalate.
Tracking Delays and Dependencies
Another challenge involves tracking delays and dependencies in the part installation process. In many cases, the smooth execution of a work order depends on several factors, including part availability, technician assignment, and even customer input. Failing to monitor these dependencies can lead to unforeseen delays, resulting in inefficient service and increased operational costs.
One effective method to address this issue is to implement a robust project management strategy. Applying tools like Asana or Trello can help teams visualize tasks, set deadlines, and monitor progress. These tools often come with features that allow for dependency tracking. For instance, if a part is delayed in shipment, teams can quickly adjust timelines and notify all relevant parties. This proactive approach ensures that everyone understands their responsibilities and deadlines, leading to smoother operations.
"Effective management of work orders requires careful attention to detail and excellent communication between teams."
In summary, addressing miscommunication and tracking delays are crucial for optimizing the workflow related to work orders in the automotive industry. By implementing effective communication systems and project management tools, businesses can significantly reduce errors, enhance productivity, and ultimately improve customer satisfaction.
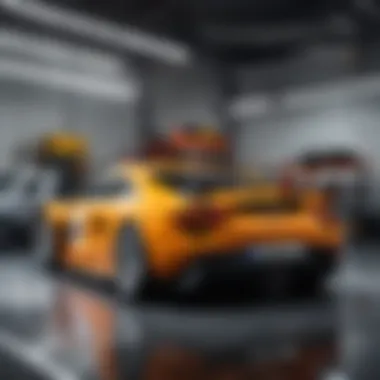
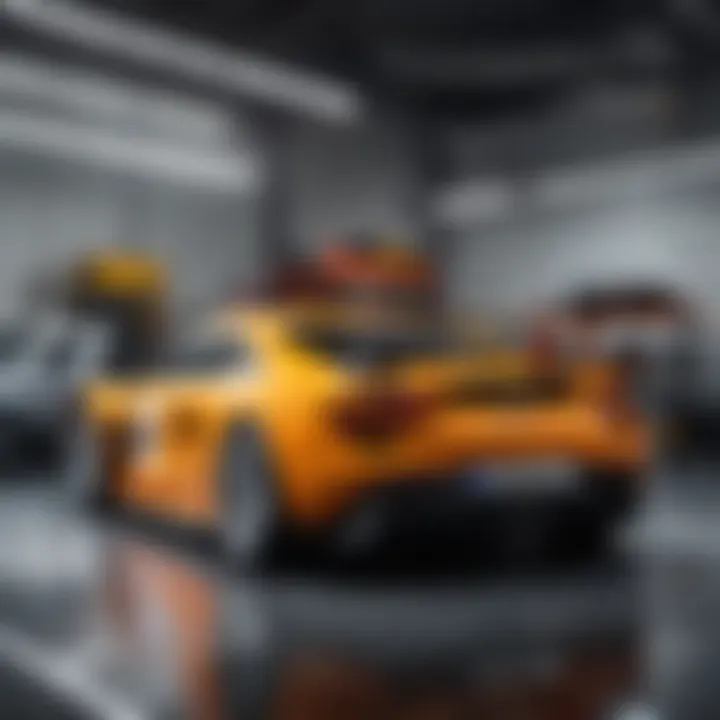
Case Studies of Work Order Implementation
Analyzing case studies related to work order implementation is vital for understanding the practical aspects that can affect efficiency and accuracy in automotive services. Through real-world scenarios, it becomes easier to identify success factors and pitfalls that can inform best practices in creating work orders for part installations. These case studies provide insights into how various organizations implement their work order systems, the challenges they encounter, and how they overcome them. Learning from actual implementations allows professionals in the field to streamline their own processes and improve overall service quality.
Successful Work Order Examples
Successful work orders provide tangible proof of effective management practices within auto repair environments. For instance, consider a well-known automotive repair shop that adopted a comprehensive work order system. The shop implemented detailed specifications regarding the parts required, technician assignments, and estimated completion times.
- Clear Documentation: All necessary parts were clearly listed, reducing order mistakes. This also included detailed instructions for installation.
- Efficient Workflow: The organization assigned technician roles based on specialization and experience, resulting in faster repair times.
- Real-Time Updates: By using a cloud-based system, the shop tracked progress and communicated updates to both technicians and customers effectively.
The shop's improved customer satisfaction scores exemplified the positive impact of a well-implemented work order system.
Lessons Learned from Failures
Examining failures in work order implementation can reveal significant lessons that help prevent future issues. One notable case involved an automotive service center that neglected proper communication regarding part availability.
- Lack of Verification: The team did not confirm part availability before scheduling installation. As a result, vehicles were often left waiting for parts that were not in stock.
- Delayed Work Orders: This failure to check stock before creating work orders led to delays, increasing customer dissatisfaction.
- Inconsistent Documentation: The notes on work orders were not consistently detailed, which caused confusion among technicians leading to installation mistakes.
This scenario highlights the importance of clear communication, stock verification, and thorough documentation. Each of these lessons underscores the critical elements necessary for effective work order creation and management, emphasizing the need for methodical approaches in automotive services.
Future Trends in Work Order Management
The landscape of work order management in the automotive industry is evolving rapidly. Understanding future trends is crucial for maintaining competitiveness and efficiency. The integration of new technologies, shifting customer expectations, and the demand for enhanced productivity drive these changes. Staying ahead in this area not only benefits the operational aspects but also aligns with the strategic goals of the organization.
The Role of Automation and AI
Automation is transforming how work orders are created, managed, and fulfilled. With the advancement of Artificial Intelligence (AI), tasks that were once manual and time-consuming are becoming streamlined. For example, automated systems can generate work orders based on historical data of repairs needed, inventory levels, and customer requests. This reduces human error and speeds up the process significantly.
Moreover, AI can analyze patterns in work order data to predict future needs. This predictive capability allows for better resource allocation and inventory management. By utilizing automation and AI, automotive businesses can not only improve their efficiency but also enhance customer satisfaction through quicker service delivery.
Key benefits of adopting automation and AI include:
- Increased Efficiency: Automated processes reduce the time and effort needed to manage work orders.
- Enhanced Accuracy: Reduces errors related to manual input.
- Predictive Insights: AI can analyze data trends to forecast future requirements.
Evolving Industry Standards
The automotive industry is heavily influenced by regulatory changes and technological advancements. As standards evolve, so too must work order management practices. Staying compliant with new regulations related to safety and environmental concerns is essential. This requires continuous updates to work order templates and processes to ensure they meet current standards.
The embrace of digital tools is also setting new industry benchmarks. Platforms that provide users with mobile capabilities, online tracking, and real-time updates are becoming more standard. Organizations that adapt to these changes can improve communication between teams, ensuring everyone is on the same page.
As industry standards shift, companies must:
- Regularly Update Processes: Adapt procedures to align with new regulations and technologies.
- Invest in Training: Ensure staff are knowledgeable about new systems and standards.
- Monitor Industry Trends: Keep abreast of changes affecting work order management.
The future of work order management is not merely about keeping up, but about leading in innovation and efficiency.
In summary, the future trends in work order management present significant opportunities for improvement. Automation and AI are pivotal in enhancing efficiency and accuracy. Simultaneously, evolving industry standards necessitate a proactive approach to training and process adaptation. By understanding and embracing these changes, automotive professionals can position themselves for success.
The End
In this article, we have explored the multifaceted process of creating a work order for part installation in the automotive industry. The significance of this topic cannot be understated. Work orders serve as the backbone of efficient service operations, ensuring that necessary tasks are completed systematically and accurately. They facilitate communication between departments, provide a clear roadmap for technicians, and optimize resource allocation.
Key benefits of an effective work order include:
- Precision: Clarity in the details minimizes errors in part installation and procedure execution.
- Efficiency: A well-structured work order streamlines workflow and reduces downtime.
- Accountability: Establishment of responsibilities clarifies who is in charge of specific tasks, which enhances performance management.
- Tracking: Work orders allow for easy monitoring of progress and enable timely updates regarding the installation process.
Considerations when finalizing a work order include:
- Ensuring all relevant information is thoroughly documented.
- Regular follow-ups to track completion and address any issues that may arise.
- Integrating new technologies to enhance the efficiency of work order management.
The importance of crafting a meticulous work order is underscored by its role in enhancing service quality and customer satisfaction. In closing, a detailed, well-documented work order will not only lead to successful part installations but will also contribute to the overall success of automotive service operations. It is evident that investing time and resources in perfecting this process pays dividends in operational excellence.
"The key to successful automotive service lies in precision, accountability, and efficient work order management."
For additional resources, consider visiting Wikipedia, Britannica, Reddit, or Facebook for further insights and discussions.